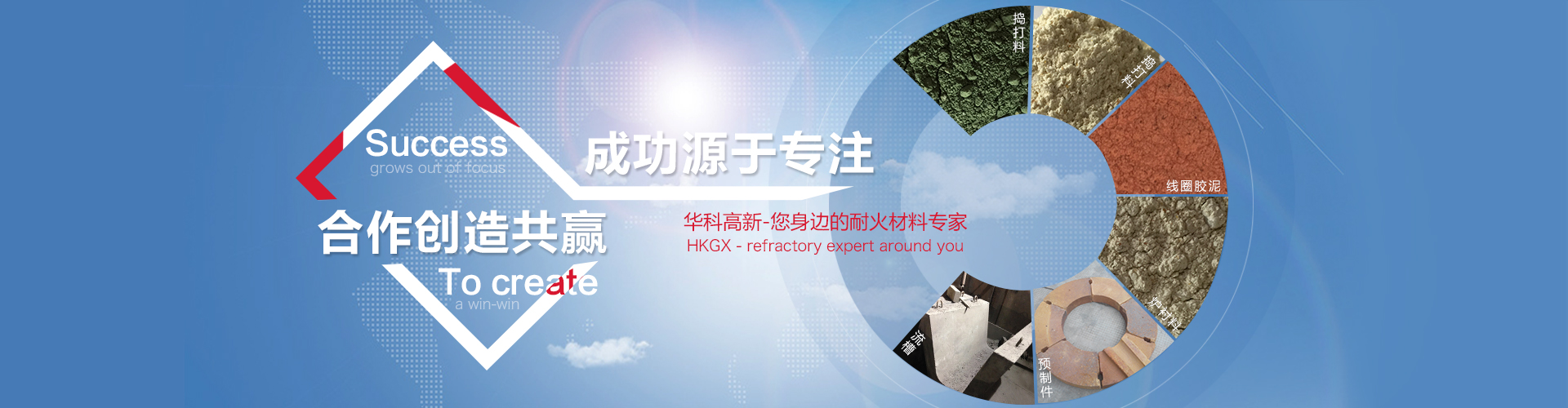
INTRODUCTION OF FURNACES AND REFRACTORIES
This section introduces furnaces and refractories and explains the various design and operation aspects.
1.1 What is a furnace?
A furnace is an equipment used to melt metals for casting or to heat materials to change their shape (e.g. rolling, forging) or properties (heat treatment).
Since flue gases from the fuel come in direct contact with the materials, the type of fuel chosen is important. For example, some materials will not tolerate sulphur in the fuel. Solid fuels generate particulate matter, which will interfere the materials placed inside the furnace. For this reason:
Most furnaces use liquid fuel, gaseous fuel or electricity as energy input.
Induction and arc furnaces use electricity to melt steel and cast iron.
Melting furnaces for nonferrous materials use fuel oil.
Oil-fired furnaces mostly use furnace oil, especially for reheating and heat treatment of materials.
Light diesel oil (LDO) is used in furnaces where sulphur is undesirable.
Furnace ideally should heat as much of material as possible to a uniform temperature with the least possible fuel and labor. The key to efficient furnace operation lies in complete combustion of fuel with minimum excess air. Furnaces operate with relatively low efficiencies (as low as 7 percent) compared to other combustion equipment such as the boiler (with efficiencies higher than 90 percent. This is caused by the high operating temperatures in the furnace. For example, a furnace heating materials to 1200 oC will emit exhaust gases at 1200 oC or more, which results in significant heat losses through the chimney.
All furnaces have the following components as shown in Figure 1 (Carbon Trust, 1993):
Refractory chamber constructed of insulating materials to retain heat at high operating temperatures.
Hearth to support or carry the steel, which consists of refractory materials supported by a steel structure, part of which is water-cooled.
Burners that use liquid or gaseous fuels to raise and maintain the temperature in the chamber. Coal or electricity can be used in reheating furnaces.
Chimney to remove combustion exhaust gases from the chamber
Charging and discharging doors through which the chamber is loaded and unloaded. Loading and unloading equipment include roller tables, conveyors, charging machines and furnace pushers.
1.2 What are refractories?
Any material can be described as a ‘refractory,’ if it can withstand the action of abrasive or corrosive solids, liquids or gases at high temperatures. The various combinations of operating conditions in which refractories are used, make it necessary to manufacture a range of refractory materials with different properties. Refractory materials are made in varying combinations and shapes depending on their applications. General requirements of a refractory material are:
Withstand high temperatures
Withstand sudden changes of temperatures
Withstand action of molten metal slag, glass, hot gases, etc
Withstand load at service conditions
Withstand load and abrasive forces
Conserve heat
Have low coefficient of thermal expansion
Should not contaminate the material with which it comes into contact
Table 1 compares the thermal properties of typical high density and low density refractory materials.
Table 1. Typical Refractory Properties (The Carbon Trust, 1993)
Property |
High Thermal Mass |
Low Thermal Mass (Ceramic fiber) |
Thermal conductivity (W/m K) |
1.2 |
0.3 |
Specific heat (J/kg K) |
1000 |
1000 |
Density (kg/m3) |
2300 |
130 |
Depending on the area of application such as boilers, furnaces, kilns, ovens etc, temperatures and atmospheres encountered different types of refractories are used. Typical installations of refractories are shown in Figure 2.
Figure 2a. Refractory lining of a furnace Figure 2b. Refractory walls of a furnace arch (BEE, 2005)
interior with burner blocks (BEE, 2005)
Some of the important properties of refractories are:
Melting point: Pure substances melt instantly at a specific temperature. Most refractory materials consist of particles bonded together that have high melting temperatures. At high temperatures, these particles melt and form slag. The melting point of the refractory is the temperature at which a test pyramid (cone) fails to support its own weight.
Size: The size and shape of the refractories is a part of the design of the furnace, since it affects the stability of the furnace structure. Accurate size is extremely important to properly fit the refractory shape inside the furnace and to minimize space between construction joints.
Bulk density: The bulk density is useful property of refractories, which is the amount of refractory material within a volume (kg/m3). An increase in bulk density of a given refractory increases its volume stability, heat capacity and resistance to slag penetration.
Porosity: The apparent porosity is the volume of the open pores, into which a liquid can penetrate, as a percentage of the total volume of the refractory. This property is important when the refractory is in contact with molten charge and slag. A low apparent porosity prevents molten material from penetrating into the refractory. A large number of small pores is generally preferred to a small number of large pores.
Cold crushing strength: The cold crushing strength is the resistance of the refractory to crushing, which mostly happens during transport. It only has an indirect relevance to refractory performance, and is used as one of the indicators of abrasion resistance. Other indicators used are bulk density and porosity.
Pyrometric cones and Pyrometric cones equivalent (PCE): The ‘refractoriness’ of (refractory) bricks is the temperature at which the refractory bends because it can no longer support its own weight. Pyrometric cones are used in ceramic industries to test the refractoriness of the (refractory) bricks. They consist of a mixture of oxides that are known to melt at a specific narrow temperature range. Cones with different oxide composition are placed in sequence of their melting temperature alongside a row of refractory bricks in a furnace. The furnace is fired and the temperature rises. One cone will bends together with the refractory brick. This is the temperature range in oC above which the refractory cannot be used. This is known as Pyrometric Cone Equivalent temperatures. (Figure 3)
Creep at high temperature: Creep is a time dependent property, which determines the deformation in a given time and at a given temperature by a refractory material under stress.
Volume stability, expansion, and shrinkage at high temperatures: The contraction or expansion of the refractories can take place during service life. Such permanent changes in dimensions may be due to:
The changes in the allotropic forms, which cause a change in specific gravity
A chemical reaction, which produces a new material of altered specific gravity
The formation of liquid phase
Sintering reactions
Fusion dust and slag or by the action of alkalies on fireclay refractories, to form alkalialumina silicates. This is generally observed in blast furnaces.
Reversible thermal expansion: Any material expands when heated, and contracts when cooled. The reversible thermal expansion is a reflection on the phase transformations that occur during heating and cooling.
Thermal conductivity: Thermal conductivity depends on the chemical and mineralogical composition and silica content of the refractory and on the application temperature. The conductivity usually changes with rising temperature. High thermal conductivity of a refractory is desirable when heat transfer though brickwork is required, for example in recuperators, regenerators, muffles, etc. Low thermal conductivity is desirable for conservation of heat, as the refractory acts as an insulator. Additional insulation conserves heat but at the same time increases the hot face temperature and hence a better quality refractory is required. Because of this, the outside roofs of open-hearth furnaces are normally not insulated, as this could cause the roof to collapse. Lightweight refractories of low thermal conductivity find wider applications in low temperature heat treatment furnaces, for example in batch type furnaces where the low heat capacity of the refractory structure minimizes the heat stored during the intermittent heating and cooling cycles. Insulating refractories have very low thermal conductivity. This is usually achieved by trapping a higher proportion of air into the structure. Some examples are:
Naturally occurring materials like asbestos are good insulators but are not particularly good refractories
Mineral wools are available which combine good insulating properties with good resistance to heat but these are not rigid
Porous bricks are rigid at high temperatures and have a reasonably low thermal conductivity.